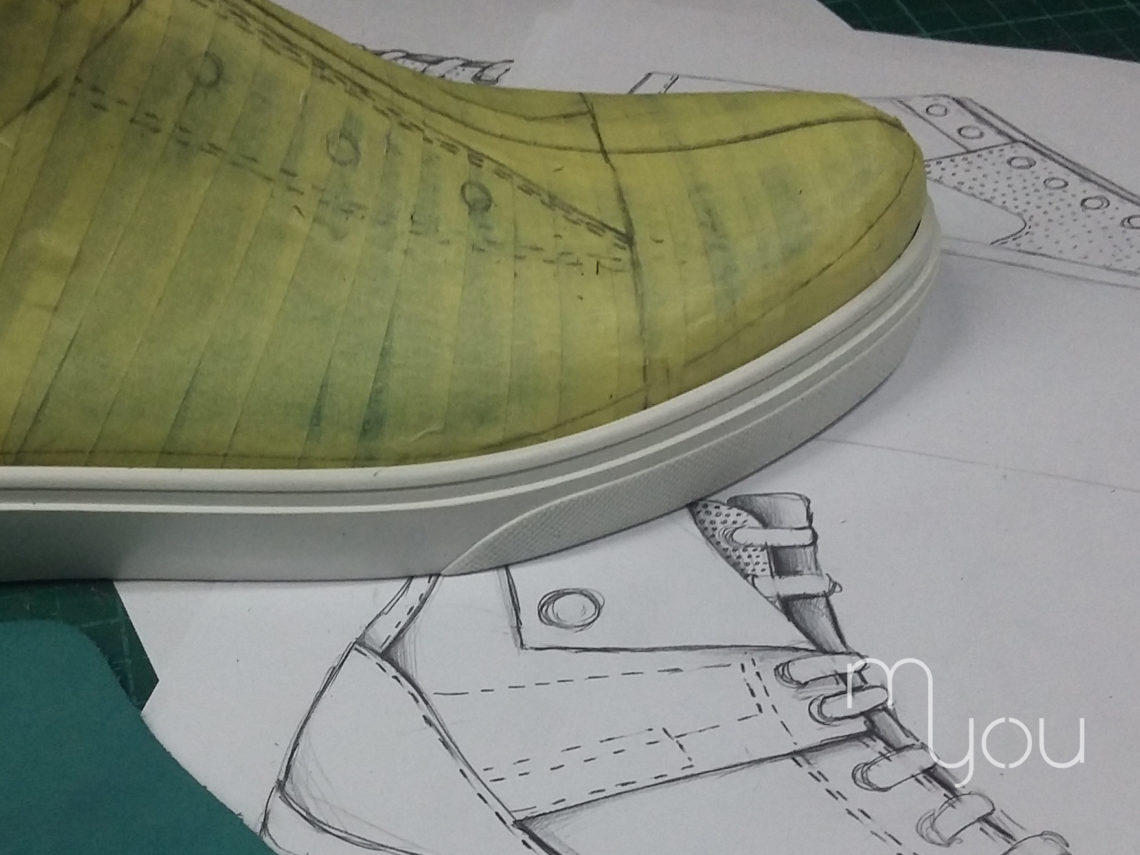
Historia jednej pary – jak powstają buty
Dziś chciałabym zabrać Was w wyjątkowe miejsce. Tam, gdzie rodzi się pomysł, zostaje zrealizowany, zapakowany w pudełka i wysłany do wielu zakątków świata. Zapraszam Was w podróż po fabryce obuwia, w której przez ostatni miesiąc miałam przyjemność odbywać staż. Dzięki uprzejmości wielu osób mogłam przygotować materiał filmowy, w celu pokazania całego procesu powstawania butów, które zaprojektowałam…dla siebie. Opowiem na początku o kilku ważnych kwestiach, które z pewnością pozwolą na lepszy odbiór materiału filmowego.
Wracając jeszcze do tematu z poprzedniego artykułu dotyczącego pomiaru długości stopy chciałam wspomnieć o pewnej zależności. W jednej z książek znalazłam rysunek, który świetnie pokazuje jak wydłuża się stopa podczas wykonywania ruchu względem ułożenia stopy w spoczynku. „Przy oderwaniu się pięty od płaszczyzny palce stopy wydłużają się i wystają poza przednią krawędź czubka spodu.” [1] Dlatego tak ważne jest aby podczas mierzenia obuwia w sklepie przejść się kilka kroków w celu sprawdzenia dopasowania.
Swoją pracę rozpoczęłam od wizyty w magazynie, gdzie wybrałam komponenty oraz dodatki (kopyto w odpowiednim rozmiarze, podeszwę, sznurowadła, oczka, nity) pamiętając o tym, że…
Miałam możliwość przymierzenia wcześniejszych wzorów przygotowanych na wybranym przeze mnie kopycie. Gdyby jednak nie było to możliwe pomiaru mogłabym dokonać w sposób, o którym pisałam poprzednio. Kopyto stanowi jeden z najważniejszych czynników w produkcji obuwia. Na nim powstaje koncepcja podziału cholewki oraz jej formowanie podczas montażu. Jego forma decyduje o kształcie obuwia. Do stworzenia formy wykonuje się szereg pomiarów stopy – musi ono uwzględniać ruch wykonywany przez stopę podczas chodzenia. Podeszwy są przypisane do konkretnego kopyta. To samo tyczy się obcasów, szczególnie ich wysokości. Duże znaczenie w tym wypadku ma skłon kopyta czyli wzniesienie czubka i pięty. „Do końca ubiegłego wieku obuwie dla prawej i lewej strony stopy wykonywano na jednym kopycie symetrycznym. Kopyta asymetryczne zaczęto wytwarzać na podstawie opracowanych wytycznych dotyczących kształtu podeszwy odpowiadającej stopie.”[2]
Wybór kopyta warunkują nie tylko tendencje, ale przede wszystkim przeznaczenie obuwia. Kopyta do obuwia męskiego ciężkiego np. roboczego, wojskowego powinno zapewnić stopie wygodę, przede wszystkim w przedstopiu i czubku ze względu na wymóg największej swobody w czasie pracy mięśni w tym miejscu. Obuwie wyjściowe jest zaś szczuplejsze, ma węższe czubki i nieco wcięte boki, z reguły na obcasie. Dla butów przeznaczonych do górskich wycieczek stosuje się kopyta z wyższym wzniesieniem czubka, w celu ułatwienia ruchu, szczególnie podczas schodzenia. Podobnie w obuwiu narciarskim z tą różnicą, że wzniesienie czubka jest mniejsze, a sam czubek ścięty dla lepszego mocowania. Buty z wysoką cholewką wymagają obszerniejszej pięty. W czółenkach ważny jest kształt czubka, górna część podbicia oraz pięta. W tym przypadku cholewka musi dobrze przylegać do stopy. W obuwiu codziennego użytku stawia się przede wszystkim na komfort, dlatego preferuje się kopyta szersze i płaskie. Inaczej też wyglądają kopyta do obuwia niemowlęcego (szeroki czubek, wąska pięta) i dziecięcego (lekkie zaokrąglenie po zewnętrznej stronie palców). Projektując należy brać pod uwagę potrzeby użytkowników, szczególnie jeśli mamy na myśli obuwie zdrowotne. W tym przypadku ważna jest tęgość (wymiar szerokości podstawy przedstopia i pięty oraz wymiar obwodu przedstopia i podbicia).[3]
Kolejnym etapem był wybór surowców. Ze wzornika wybrałam rodzaj i kolor skóry.
…..Pomysł powoli się klarował. Najpierw rozrysowałam projekt na kartce, a następnie przeniosłam go na uprzednio oklejone taśmą papierową kopyto. To pozwoliło mi zdjąć wzór i rozłożyć go „na płasko”. Bardzo dokładnie przeniosłam wszystkie części na czystą kartkę papieru uwzględniając niezbędne naddatki na zszycie oraz wykończenie.
Elementy wykroiłam ręcznie. Na co dzień projektanci wykonują te zadania przy pomocy komputera, a rozkrój odbywa się na ploterach. Tak jak podczas krojenia elementów na tkaninie należy zwrócić uwagę na kierunek nitki prostej, tak tutaj trzeba określić ich ułożenie na skórze względem układu topograficznego oraz kierunków ciągliwości.
Grubość w poszczególnych częściach jest zróżnicowana – najgrubsza w części grzbietowej, w karku cieńsza, a w tylnych łapach i części przyogonowej jest nierównomierna. Najbardziej wartościowy jest tzw. krupon ze względu na ścisłą strukturę i grubość. Jakościowo najgorszą częścią skóry są łapy i pachwiny – są luźne i bardzo ciągliwe. W części łap i zadów można zaobserwować dużą kruchość tkanki. Przede wszystkim miejsca w obuwiu, które narażone są w większym stopniu na pracę stopy, tym samym na zużycie (noski, przyszwy, paski do zapinania) powinny być wycięte z najbardziej ścisłej części skóry. Rysunek poniżej pokazuje jak układają się ciągliwości na poszczególnych partiach obuwia. Oznacza to, że skóra (a także tkanina w przypadku np. trampek) powinna je blokować i charakteryzować się ciągliwością w przeciwnym kierunku. [4]
Przy wyborze surowca należy zwrócić również uwagę na jego walory estetyczne(uszkodzenia po stronie lica). Niektóre skóry pokryte są różnego rodzajami laminatami. Stosowane są również ozdobne perforacje czyli wycinanie bądź też wyciskanie w elementach wierzchowych różnego rodzaju ozdobnych wzorów. Jest stosowana również do obuwia zdrowotnego w celu podniesienia komfortu użytkowania. Miałam możliwość wykonania perforacji na wybranej przeze mnie gładkiej skórze za pomocą gotowej matrycy.
Po wykrojeniu elementów ich brzegi są ścieniane (szarfowane) w odpowiedni sposób. Warunkuje to sposób szycia, należy zastanowić się, które krawędzie będą naszywane, które będą stanowiły spód lub też zostaną zawinięte czy zszyte „na sztorc” (czyli do zewnątrz – jest to ciekawy zabieg jeśli mizdra skóry jest w innym kolorze niż lico). Dzięki ścienianiu wyrównujemy grubość w miejscu łączenia, co wpływa na estetyczny wygląd i łatwiejsze szycie.
W kolejnym etapie przechodzimy do zszywania elementów. Maszyny słupkowewykorzystywane do szycia cholewek różnią się od stębnówki, którą wykorzystuję przy szyciu odzieży, stopką oraz „słupkiem”, od którego pochodzi nazwa. Miałam okazję kilka razy poćwiczyć szycie. Bardzo wygodne jest to, że jednym pedałem można szyć, podnosić stopkę a także automatycznie obcinać nici. Oczywiście przez pierwszych kilka minut z przyzwyczajenia szukałam kolanem dźwigni podnoszącej stopkę (w niektórych modelach maszyn do szycia odzieży pedał skonstruowany jest w ten sam sposób co w maszynie słupkowej). Większość funkcji oraz sposób nawlekania nici jest bardzo podobny. Z wielkim podziwem obserwowałam jak panie, które pomagały mi w odszywaniu wzorów sprawnie i bardzo dokładnie wykonywały swoją pracę. Wiele razy zdane były na swoje sprawne oko oraz wyczucie odległości. Równolegle przystępuje się również do klejenia odpowiednich elementów (m.in. międzypodszewki, które znajdują się między wierzchem a podszewką, podkrążki pod oczka w obuwiu wiązanym czy też pianki stosowane w językach). Klejenie elementów jest również pomocne podczas szycia. Jeśli w obuwiu występuje zamek, w pierwszej kolejności jest on przyklejany a dopiero później przyszywany. Ogromne znaczenie mają znaczniki, które nie tylko stanowią punkty kontrolne ale również wyznaczają, które elementy są naszywane na siebie, do którego momentu należy szyć, w którym momencie występuje ozdobne przeszycie czy szycie ręczne oraz miejsce wybicia oczek, nap czy nitów.
Deformacja narzędzia do wybijania oczek
Z gotową cholewką udałam się wyprofilować piętę na specjalnych maszynach, a następnie wszyć podpodeszwę z tzw. texonu. Kolejnym etapem był montaż czyli nazuwanie cholewki na kopyto, formowanie pod wpływem temperatury w piecu, przygotowanie pod naklejenie podeszwy, utrwalanie, czyszczenie wszelkich zabrudzeń powstałych w wyniku montażu, następnie woskowanie, a na końcu obszycie podeszew. Buty były prawie gotowe. Wystarczyło tylko je zasznurować i wyposażyć w wyściółkę.
Zrealizowałam jeszcze jeden wzór z myślą o sobie. Chciałam wykorzystać w swoim projekcie skórę pokrytą wyjątkowym, mieniącym się wzorem. Stworzyłam projekt półbuta. Wszystkie początkowe procesy powstawania były identyczne, jednakże wyróżniał je sposób montażu. Były one ćwiekowane. Formowanie pięty odbywało się na bardzo podobnych maszynach co poprzednio jednakże wynik tych działania był inny.
Formowanie „na gorąco”
Utrwalanie kształtu „na zimno”
Tym razem nie został wszyty texon a nosek uformowany został na specjalnej maszynie po czym cholewka została połączona z podpodeszwą. Reszta procesów była taka sama jak w poprzednim przypadku. Wszystko do zobaczenia na filmie.
Podczas mojego miesięcznego stażu udało mi się wykonać kilka wzorów, niektóre w kilku wersjach kolorystycznych. Kierując się wyżej wymienionymi kryteriami w projektowaniu musiałam brać pod uwagę również odbiorcę do którego mój projekt miał zostać skierowany. Praktyka pozwoliła usystematyzować już posiadaną przeze mnie wiedzę, a także uzupełnić ją o nowe wątki. Dzięki wspaniałemu zespołowi praca była przyjemnością. A dziś przedstawiam Wam film z całego przedsięwzięcia poniżej. Jak Wam podobają się moje autorskie buty?
Pozdrawiam MJ
*Rysunki wykorzystane w artykule pochodzą z książki autorów: Liszka R., Rerutkiewicz J., Eliasz H., pt. Cholewkarstwo
[1] Liszka R., Rerutkiewicz J., Eliasz H., Cholewkarstwo, WSiP, Warszawa 1976, wyd. III, s. 51
[2] Ibidem, s.62
[3] Ibidem, s.68
[4] Ibidem, s.90

